STRUCTURAL METAL DESIGN
Structural metal design is a complex, detail-oriented, and labor-intensive process. The Customer, however, often underestimates the effect viable design solutions have on the overall construction cost. It is especially evident in the case of buildings with metal frames — due to a carefully designed and executed project, the construction cost and completion term are significantly reduced.
In order to obtain high-quality design documentation, we recommend the following:
- Engage qualified personnel (designers) with adequate practical experience
- Engage those designers that specialize in the field of structural metal design (also when metal structures are only part of the construction project)
- Clearly state the design assignment provisions
Below, the USCC staff provide detailed recommendations for the Customer as to organizational aspects of the structural design work process for maximum efficiency of project implementation.
CHOOSE YOUR STRUCTURAL METAL DESIGN SPECIALISTS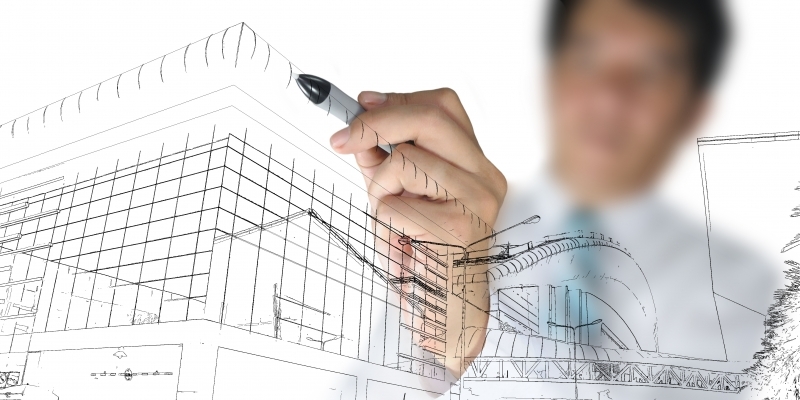
1. CHOSE A PROJECT DESIGNER
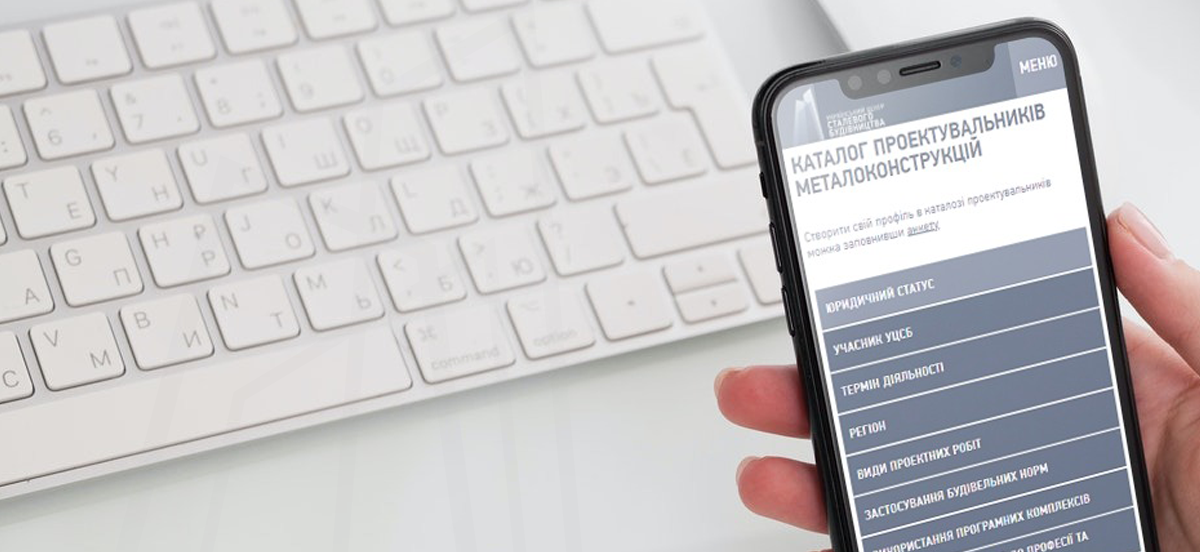
Choose one of the specialized project designers (a company or an individual) that specializes in structural metal design. For that, we offer the USCC service, and in particular, the Catalogue of structural metal designers
This service includes relevant filters and information on the main criteria crucial for the search and selection of a suitable project designer. Information on the specialty and specifics, the region of the designer's activity, work qualification and experience helps to quickly select the designer that meets the Customer's demands and requirements.
2. SPECIFIC FEATURES OF STRUCTURAL METAL DESIGN
Structural metal design has its distinct features. As a rule, designers that usually deal with concrete structures perform metal projects with significantly lower quality. Because they do not take into account the latest requirements to metal product mix, manufacturability, mounting on-site, and modern options of weight and cost optimization.
The difference in the cost of installed metal structures can be tens of times bigger than the cost of work of a designer that specializes in metals. For this reason, when you select a project designer, it is necessary to consider not only the declared design cost but also the "estimated by designer" end result - a preliminary estimate of the metal quantity and a concept solution, which shall help the Customer to calculate the cost of assembled structures at the planning stage.
Also, it is necessary to estimate the manufacture and mounting period required for the erection of the structures in question.
3. DESIGN ASSIGNMENT
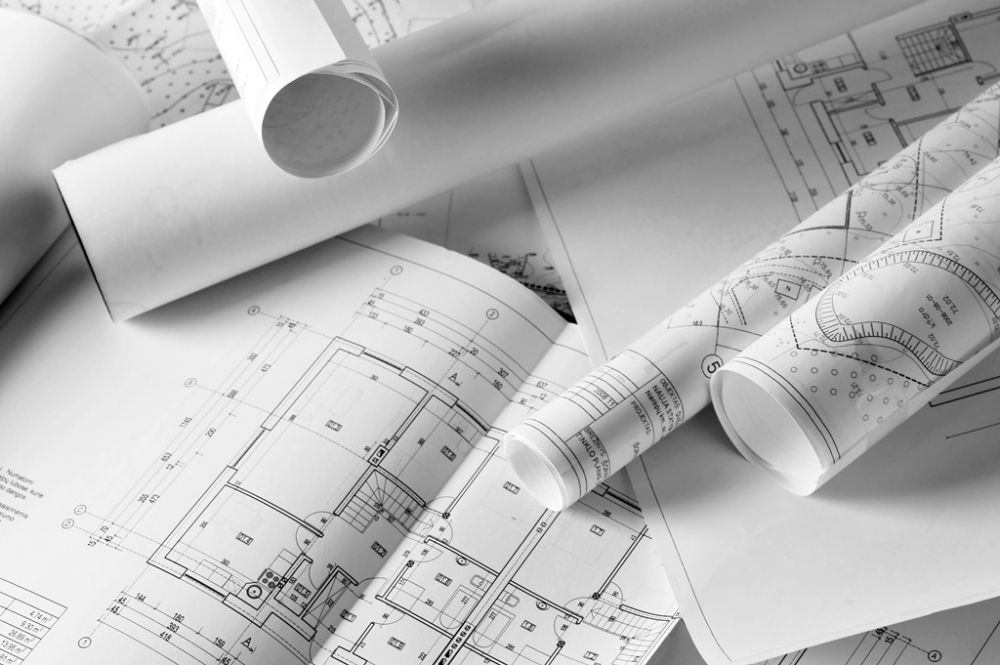
To obtain a high-quality MS, FDMS project, we recommend that the Customer should use the form of standard detailed technical assignment for structural metal design. An example of the above technical assignment can be downloaded below.
In order to reduce the construction cost, the technical design assignment shall clearly (without reserves in-store) identify the following to be utilized by the project's structural designer:
- Useful load on the frame
- Technological loads
- Materials selected for enclosure and partitions
- Covering material
If your technical assignment is detailed and clearly stated, a designer shall not factor in the "undisturbed sleep factor", i.e., the margin of safety as a precaution.
DOWNLOAD THE TECHNICAL DESIGN ASSIGNMENT4. SPECIFIC FEATURES OF A HIGH-QUALITY DESIGN PROJECT
The quality of completed design works depends on a number of factors:
- Speed and cost of erection
- General reliability and operating life of the facility
- Operating cost
- Ability to rebuild and upgrade
- Energy efficiency and ecological friendliness of the facility
Specifics of a high-quality MS project:
- Low specific metal quantity per unit (for instance, per square meter of surface area, or per other key parameters) in comparison with similar building structures. It is reached by choosing the right design solutions, trial design, efficient use of crossing structures, and application of optimized solutions (high-strength steel, composite materials, etc.)
- Adjustment for the aspects of manufacturability, transportation and on-site mounting, reasonable unification
- Selection of available rolled metal production. Available warehouse options here
More information on the quality of design solutions can be found in DSTU Structural steel for construction. An instruction on the estimation of design solutions that provides a systemic assessment for a structural metal project.
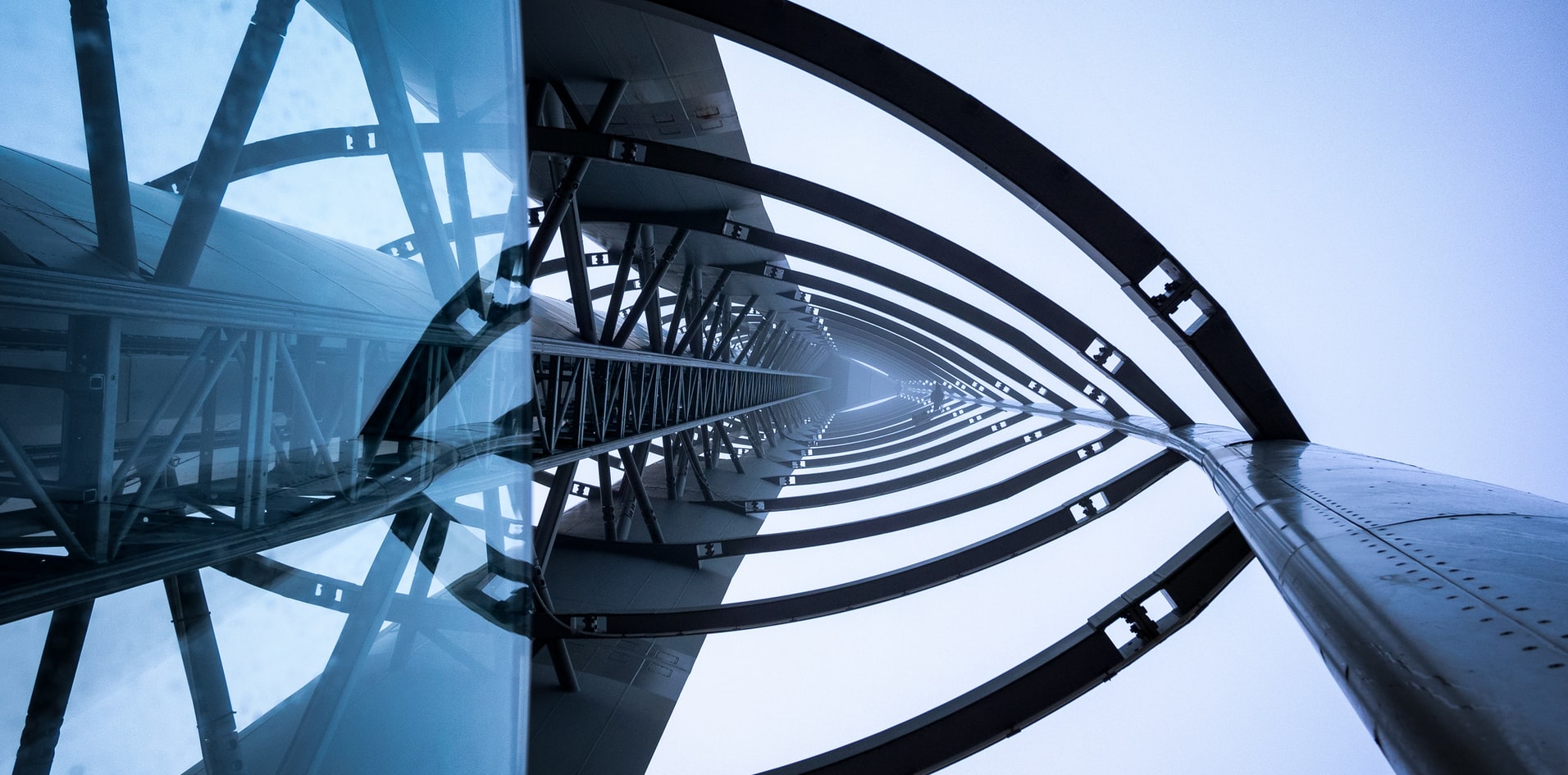
5. DESIGN STAGES
The design project is carried out in several stages depending on the designation and consequence class of the facility according to the requirements of DBN A.2.2-3:2014 Composition and content of design documentation for construction:
- Feasibility study (FS)
- Cost-benefit analysis (CBA)
- Draft project (DP)
- Project (P)
- Work project (WP)
- Work documentation (WD)
Traditionally, development of work documentation is performed in two stages:
- Drawings of metal structures (MS)
- Final shop drawings of metal structures (FDMS)
With the development of BIM-technologies, MS and FDMS development tend to combine (single-stage design): initially, a calculation model is created, then the facility is divided into subdivisions according to the mounting procedure, after which modeling and detailing up to Level LOD 400 is done by each subdivision; then, the project, wholly or partially, is submitted to one or several plants for the manufacturing of metal structures.
The MS-FDMS combination provides several advantages for the Customer:
- Cuts down the project development time by approximately 30% while improving design quality
- Significantly reduces the period required to start manufacturing and onsite mounting of metal structures
- Simplifies harmonization of "adjacent" sections of a project (AS, TC, CO)
- Simplifies operations for manufacturers and installation companies
6. RECOMMENDATIONS ON SELECTION OF A DESIGNER OF MS, FDMS PROJECTS, OR IS IT ADVISABLE TO PAY MORE FOR A DESIGN PROJECT?
As a rule, the cost of design work for the MS section depends on the "tonnage", and a tender for design is based on the lowest metal price per ton. This aproach fails to motivate a designer to apply optimization solutions and lower the weight and cost of the facility.
Recommendations on how to avoid the above situation:
- Hold tenders based on complete technical design assignments
- Demand from the project designer to indicate the intended specific amount of metal per structure, and compare only the submitted design costs, but make an assessment of the design cost and the expected cost of the facility
- Upon mutual agreement, apply price estimates that are not based on the number of tons (for instance, per 1 square meter of surface area, per 1 linear meter of span beam structures, etc.)
- Provide additional motivation for the project designer for reducing the weight of a whole facility by reducing the specific amount of metal per structure and by utilizing efficient optimized solutions
- Demand compliance with the requirements of the Regulation on design efficiency assessment
Other cost-reduction methods for the Customer by improving project efficiency are described in the article Methods of cost reduction for steel frame.
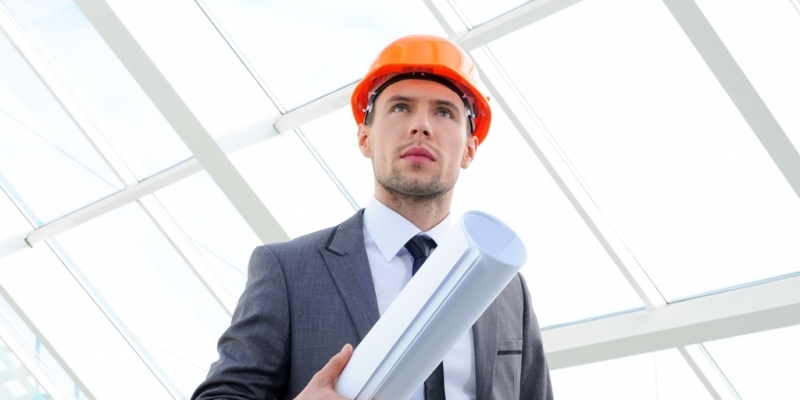