THE USCC EDUCATIONAL PROGRAM OF LEAN MANUFACTURING
The Basic LEAN program teaches the basics of lean manufacturing.
This knowledge base helps to radically change the notion on processes and methods of their assessment, to quickly obtain serious results, and to get convinced of the usefulness of the LEAN approach to management.
Only the actual involvement of the Association members can complete its tasks and accomplish its mission objectives.
Target programs and actions to stimulate the development of the steel construction sector are based on a fundamental understanding of the market problems as a whole and the problems of some representatives of the market.
The Basic LEAN program began as a response to the issue of low operating efficiency specific to most manufacturing and servicing enterprises in the sector. In the face of harsh competition and growing demands from Customer, operating management efficiency has become one of the key conditions for corporate survival.
The Association's mission is to assist companies, through the Basic LEAN program, in the training their personnel so that employees become competent and are able to manage processes in an efficient way and to increase product value and quality while cutting down costs.
The LEAN methodology, also known as Economical manufacture, has been long and successfully implemented on a global scale. This methodology is a result of research and formalization of the unique past performance of the Japanese company Toyota that could build a manufacturing system able to make products that meet customer requirements while reaching a high level of operating efficiency. The foundation of the LEAN approach lays in focusing on Customer and constant work on improvement of processes and elimination of any process-associated costs.
The formalization of Toyota's past performance afforded the opportunity to single out the main principles and tools of the LEAN methodology that enable to build efficient systems not only in the manufacturing sector but well beyond its scope: in the service, medicine, banking, educational sectors, etc.
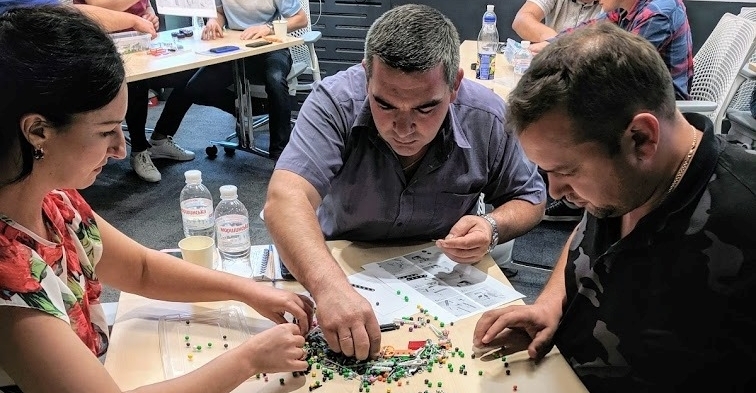
MAIN OBJECTIVES
As the educational program is being implemented, the Association sets the following objectives:
- Provide a comprehensive understanding o the methods and advantages of the LEAN approach to the management of a manufacturing enterprise
- Teach the basic tools of LEAN management
- For participants, provide the opportunity to apply the tools while lending expert support
- Make aware of the sequence of steps for implementing LEAN manufacturing tools
INTENDED USERS
The program is primarily designed for directors of manufacturing companies, heads of manufacturing departments, engineers, manufacturing technicians, and specialists, and deals with operational efficiency improvement. However, the program reaches beyond the above categories.
The program offers maximum practical focus. The Association is committed to the successful implementation of the LEAN manufacturing measures at companies that participate in the educational and training process, and expects that participants should meet the following two important requirements:
- Each participating company shall be represented by at least 2 employees. This will help to form a team responsible for further implementation of the LEAN projects at a given enterprise.
- Willingness of participants to openly discuss issues. Conducting meaningful dialogue, sharing best practices, and presenting the results of completed practical tasks enhance the usefulness of the education course and facilitate each company's business growth.
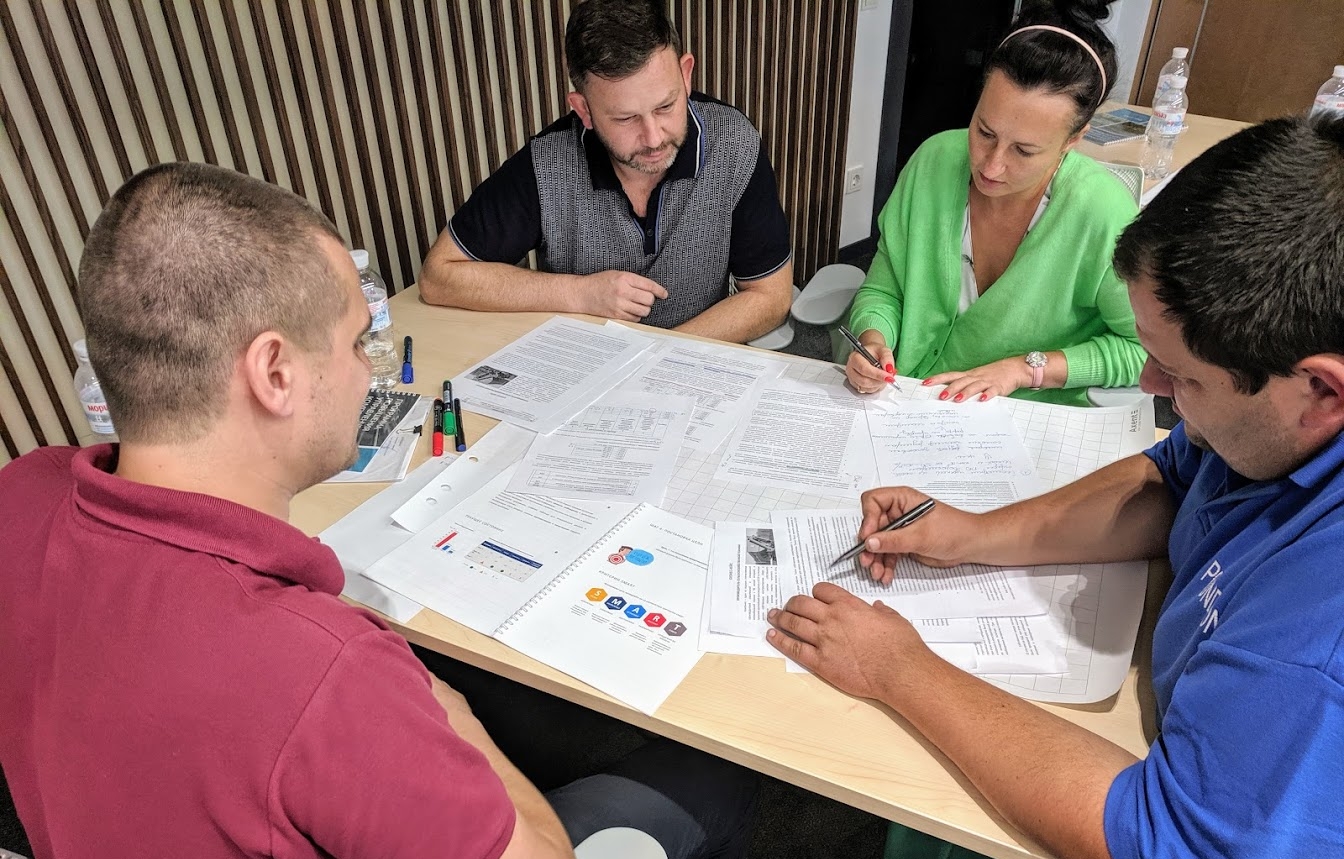
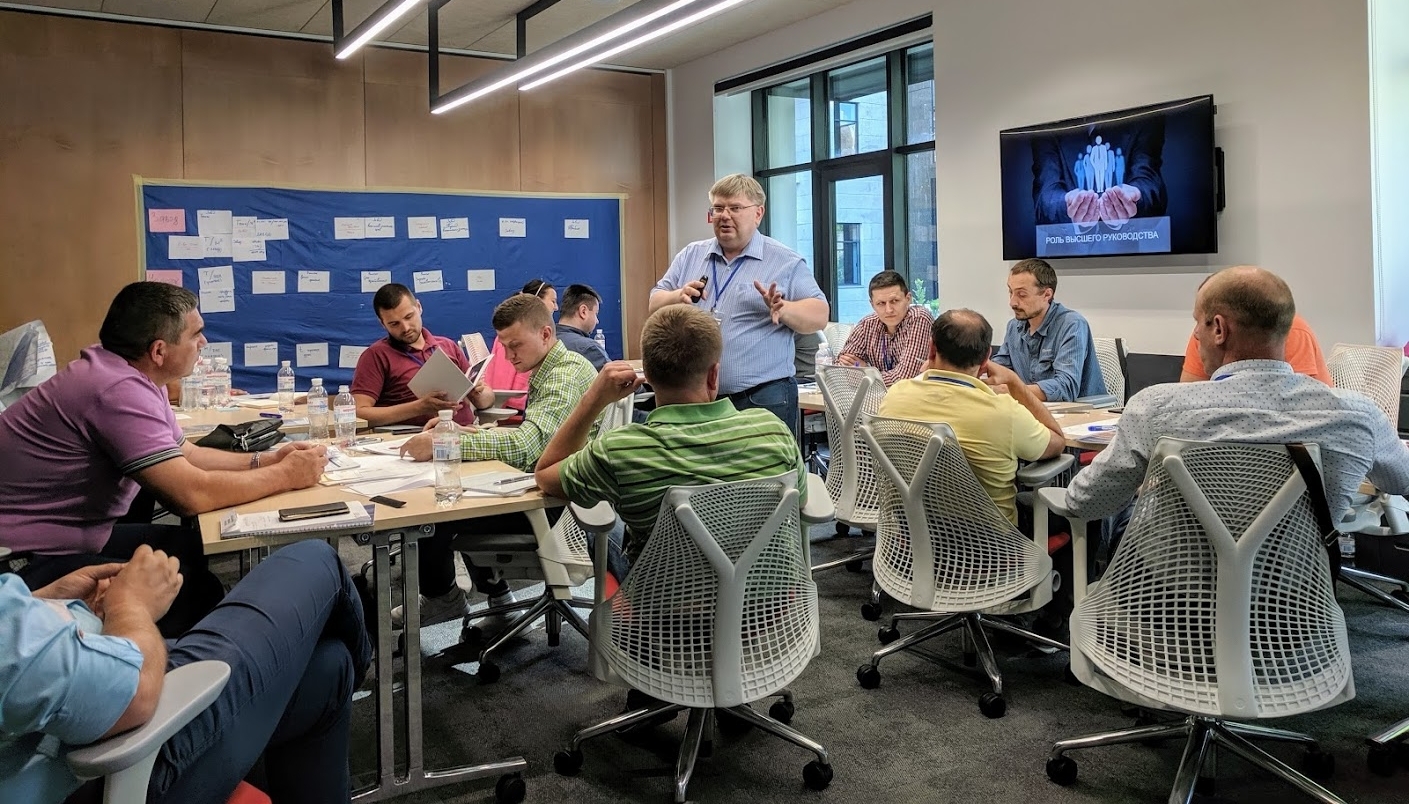
FORMAT ANS STRUCTURE OF THE EDUCATIONAL PROGRAM
The program includes 5 educational modules, each filled with the following content:
- One-day-long training sessions where theoretical material is put to practice by simulation and working on case scenarios;
- Homework on implementation of the studied LEAN manufacturing tools at the participants' companies;
- Close-group discussion of module materials;
- Consulting support from coaches until the time a module is completed, and feedback on implemented practical tasks.
After completion of their education, students shall take exam testing and defend their projects.
The program's modular system is organized in such a way that each module provides a full understanding of a given tool, and all the modules combined to demonstrate the interconnection of all tools.
LEAN MANUFACTURING TOOLS
The program presents basic concepts and tools for LEAN manufacturing in the following order:
Module 1:
TPS — Toyota production system, LEAN principles, 8 types of losses
Module 2:
Structural approach to addressing issues, Report method in A3 format
Module 3:
Visual management, 5S — a system of workplace arrangement
Module 4:
OEE — general efficiency of machinery, TPM and autonomous maintenance of machinery, SMED — the art of quick readjustment
Module 5:
VSM — value stream mapping, LEAN leadership
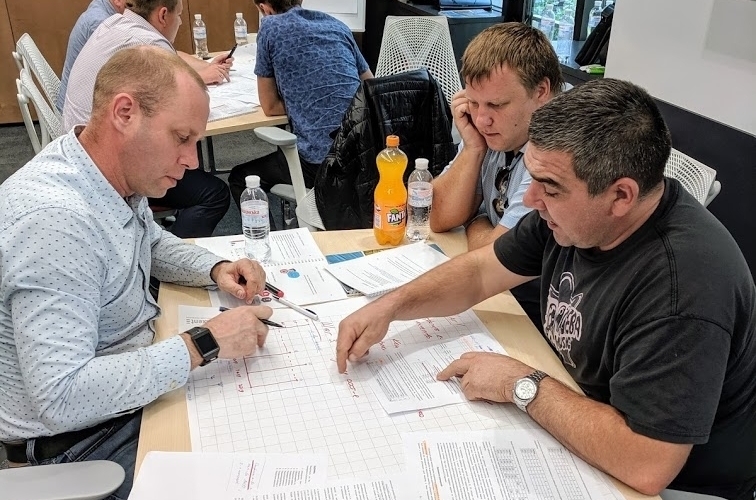
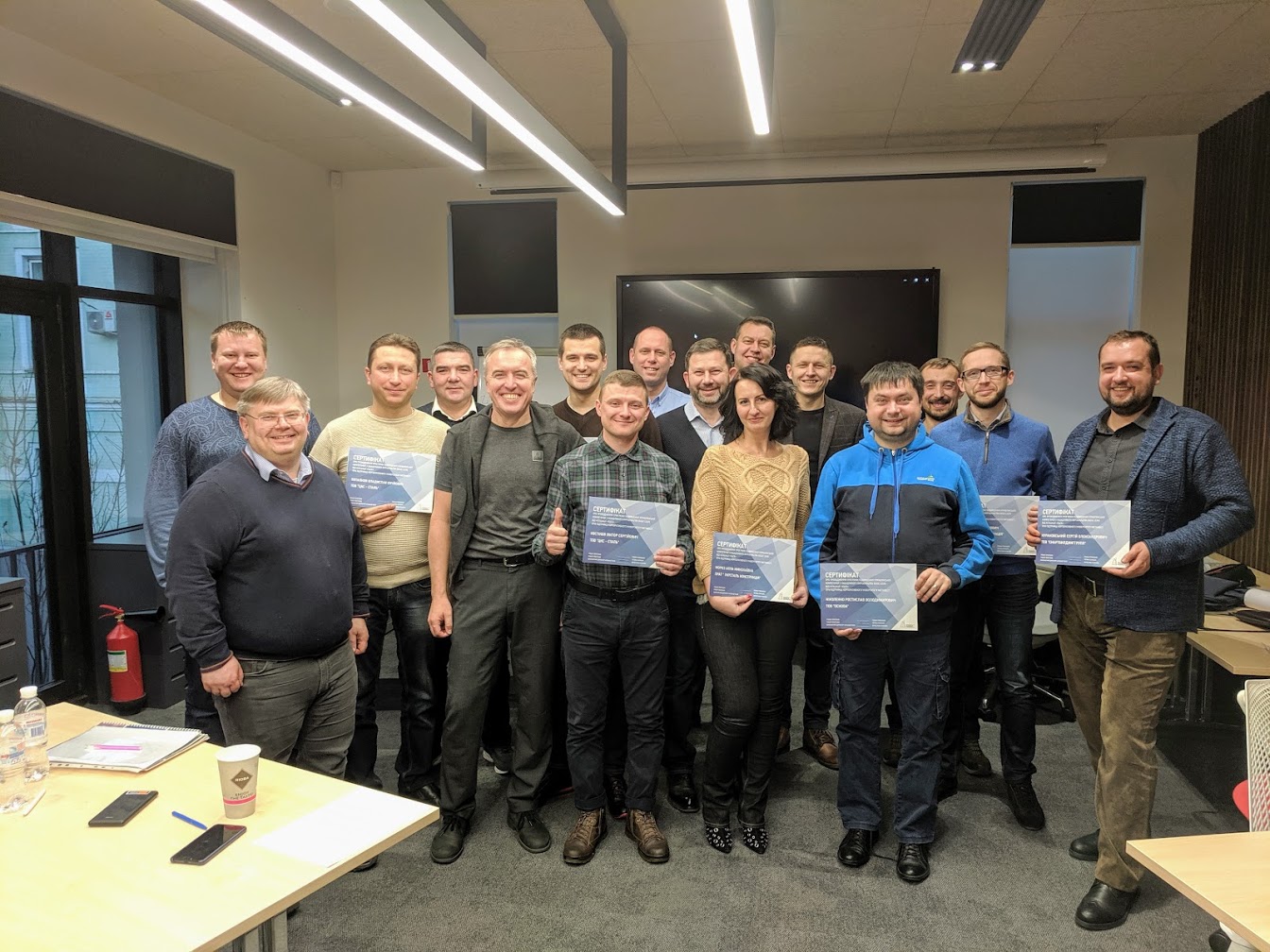
EDUCATIONAL PROGRAM PARTICIPANTS
The following companies have already become participants in the educational and training program:
- Frame Construction Centre
- Ukrsteel Construction
- Ukrsteel Construction, Zhytomir
- Ukrsteel Construction, Zaporizhia
- Ukrsteel Construction, Avdiivka
- Zhytomir Enclosure Structures Plant
- Mettransservice
- Stilko
- Staltex (Osnova Corporation)
- Smartbuidinggroup
- Heavy-Metal
- UTEM
- Dosvid-2002
- Stalex
- VZIRETS-2000
RESULTS OF IMPLEMENTING THE LEAN MANUFACTURING MEASURES
Performing practical tasks of their homework, participants have already been able to obtain actual results from implementing the LEAN methodology. Some of them are outlined below:
- Increase of the assembly line efficiency by 34%
- Increase of the production output at the pipe assembly sector by 41%
- Reduction of the assembly operation time by 32%
- Reduction of the blanking operation time by 25%
- Increase of the sheet jointing operation efficiency by 33%
- Reduction of the metal de-stacking time by 4.5 times
- Reduction of the number of flawed items manufactured with CNC equipment by 10 times
- Indirect expenses reduction by 15,7%
To register for the educational course, one must fill out a registration application.
Additional information on the program can be obtained from the learning course adviser by calling +380674095564
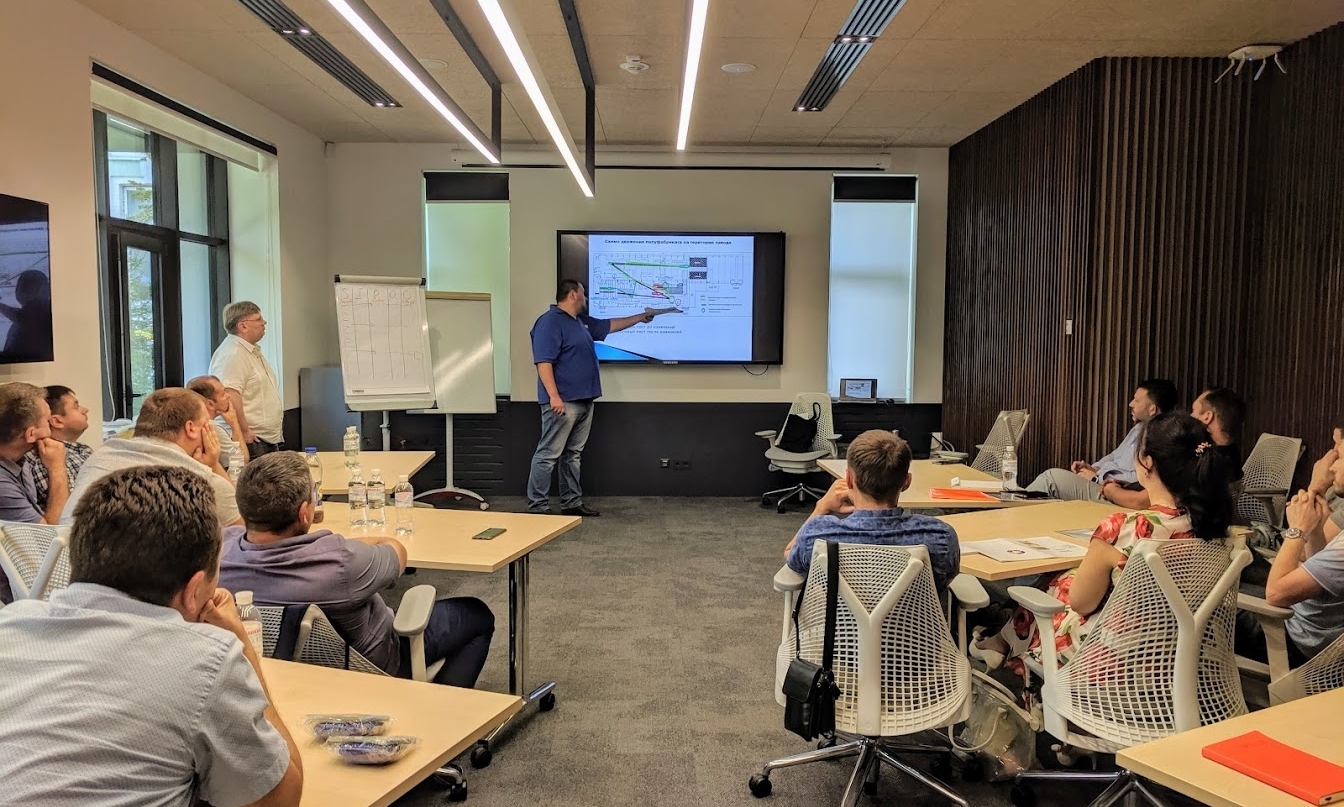