EFFICIENT STEEL SOLUTIONS FOR CAR PARK CONSTRUCTION IN A MEGAPOLIS
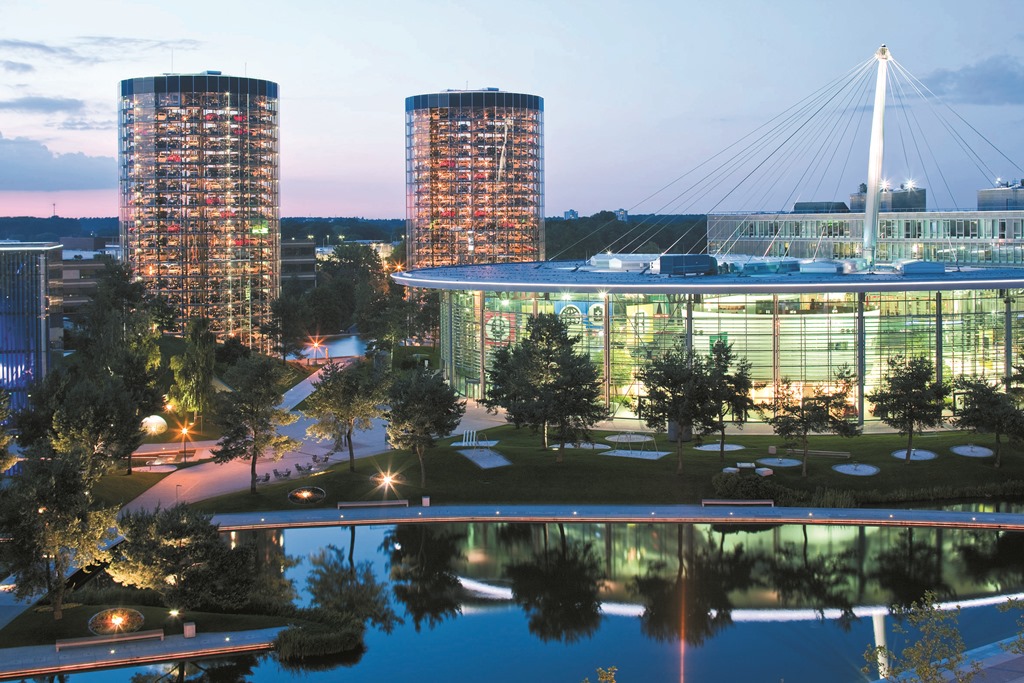
CAR PARKS IN A MEGAPOLIS
European practices demonstrate that the best way of addressing the street traffic congestion issue is to develop the infrastructure of multilevel car parking, which, in a short period, increases the number of parking spots in a city, while giving the green light to developers to make profitable investments into this prospective sector of commercial real estate.
The use of framed steel car parks in construction provides an opportunity for an investor to get up to 10% of additional parking spots* due to an increased span width and a smaller cross-section of columns, to cut down the construction time by up to 45%, and to increase the net present value (NPV) of an operating facility because of simplicity, lightness, and high factory readiness of structures.
*As compared with the traditional parking frames made of reinforced concrete.
TYPES OF MULTILEVEL CAR PARKS
The organization of above-ground single-level car parks requires a lot of lands to be allotted and worsens the existing city-planning environment. Underground multilevel car parks have limited usefulness as their construction is associated with a complex and labor-intensive zero cycle, has a negative effect on the neighboring buildings, and can necessitate relocation of the existing engineering networks.
The most optimal way to enhance the parking infrastructure of modern cities is to build multilevel above-ground car parks.
Multilevel above-ground car parks
Are most widespread in Western Europe as the optimal solution for car slots increase in a restrained urban environment. Depending on the present business needs and the construction site capacities, multilevel car parks can stand alone or be attached to, or built-in, a given building.
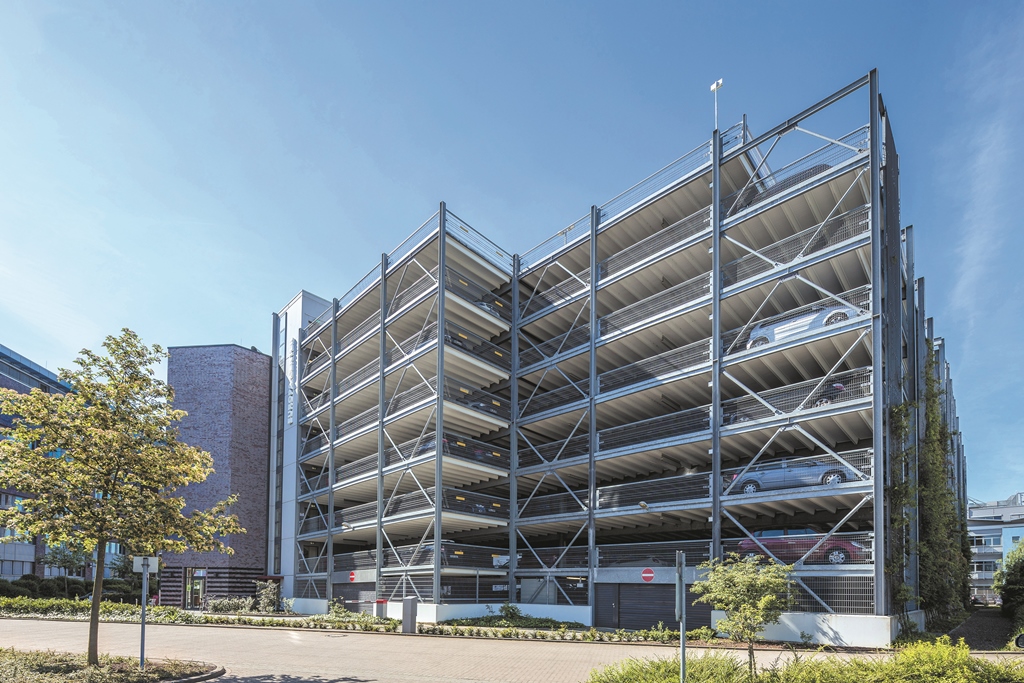
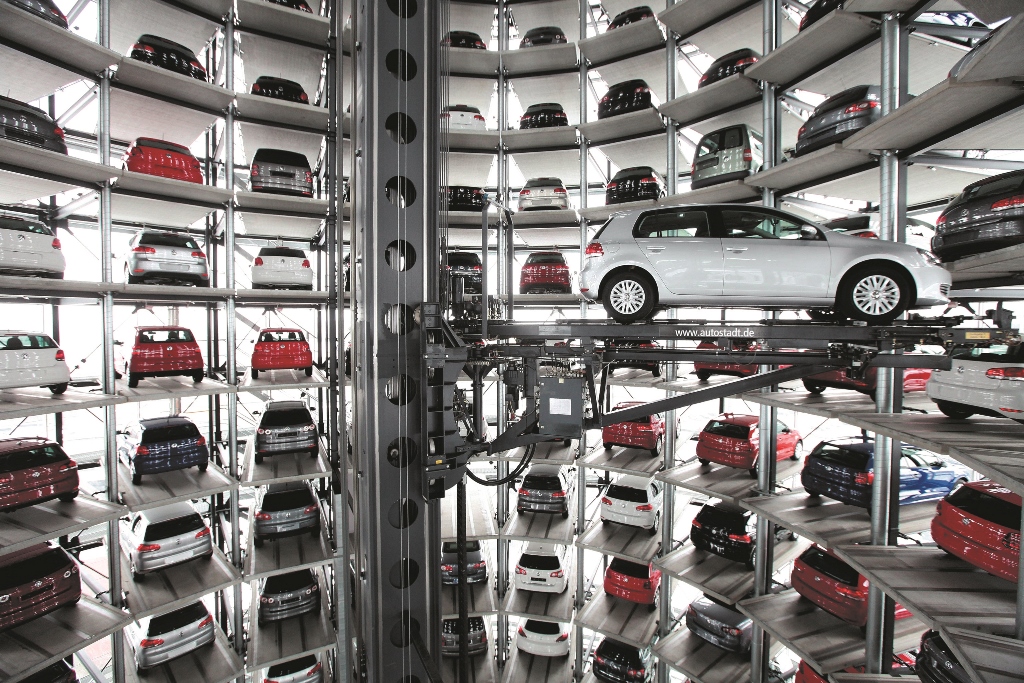
Automatic car parks
Are one of the prospective types. They demonstrate such advantages as saving time on entrance-exit-search for an available spot and ensuring safe car storage. This type of parking requires no ramps or car passageways, which means more (by 35%-50%) parking slots as compared to other construction techniques. At the same time, a complex way the car owner has to face while accessing their vehicle placed in automatic parking does limit the use of this type of facilities in shopping facilities, entertainment, and office centers, as well as in other locations that require car access without leaving the parking slot.
Mechanized car parks (semiautomatic)
Is a simplified version of automatic parking, which is a temporary rapid construction, often to concentrate surface car parks. Automatic and mechanized car parks can stand alone or be attached to, or built-in, an existing building; they also can be located underground.
ADVANTAGES OF STEEL CAR PARKS
Construction of multilevel car parks of metal structures in comparison with reinforced concrete allows the developer to obtain a number of undeniable advantages, such as reducing the time and cost of construction, increasing the number of parking spaces per unit area, adaptability in subsequent reconstructions and additions, the possibility of maximum integration into the existing architectural environment.
A detailed comparison between the use of steel and monolithic reinforced concrete for the erection of car parks can be done using two design schemes of a simulated project for an open three-level car park.
.jpg)
Rapid construction
The construction completion time is cut down by up to 45% if a multilevel car park is erected with the use of metal structures instead of reinforced concrete. This is due to high factory readiness and unification of metal structures, simplicity of installation under restrained urban conditions. Large span, little weight, and a small number of frame items increase technological effectiveness of installation and decrease the foundation dimensions, which in turn speeds up the construction process. Reduction of the construction completion time lowers the expenses on land maintenance and increases the NPV (net present value) due to earlier commissioning.
An up to 10%-increase of parking slots
As there are no additional columns required with the span of 15 m—18 m and the column dimensions are small compared to reinforced concrete pillars, it means an up to 10%-increase of parking slots and a more convenient scheme of car movement.
Saving of construction expenses
As compared with reinforced concrete, the weight of a steel-made building is decreased by 40% - 60%, which lowers the cost of foundations for multilevel car parks by 15%—20% of the general construction project cost.
Simple expansion and reconstruction
Steel structures frames have high repairability and flexibility during retrofitting, adding structures, reconstruction, and changes of the building's functional profile. The use of hinged beam-column joints fully unifies the unit flooring solution and makes it possible to reuse such joints, providing mobility and ecological safety of the construction process.
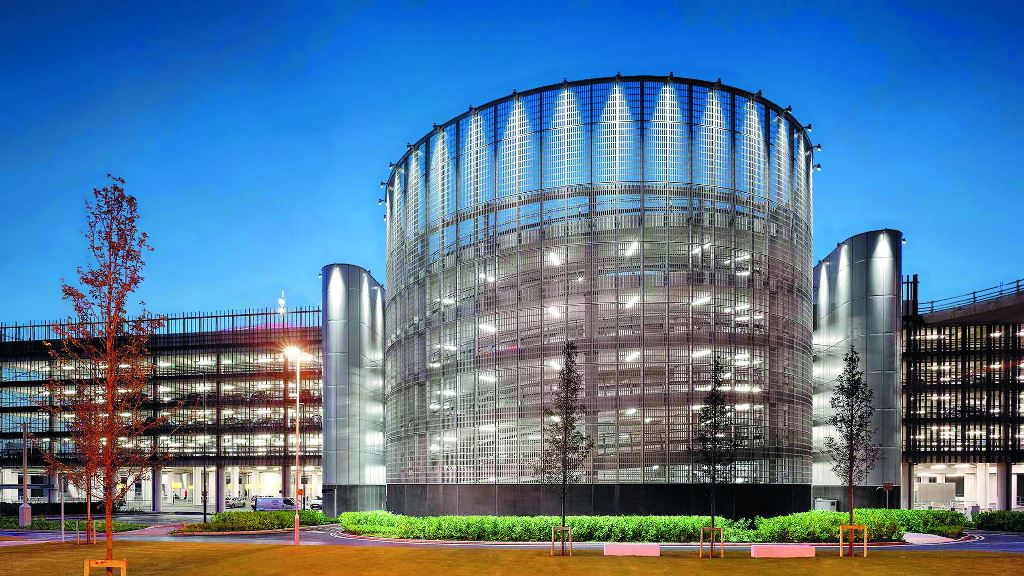
.jpg)
Easy installation work in limited space
Due to unification of design solutions, high factory readiness, and the absence of "wet" processes under restrained urban conditions, the use of metal structures helps to complete a project within a minimal period, with no threat to the functioning of adjacent buildings, and without any traffic or road congestion issues.
Creation of landmark architectural structures
Today's advanced technologies of design and manufacture of steel frames and enclosure structures provide broad options for creating a unique multilevel parking architecture, and for its integration into the existing urban architectural space. A broad palette of coatings, weather-resistant grades of steel, decorative and fencing metal panels, etc. help to reach the necessary expressiveness of the external appearance of car parks.
SPECIFICS OF CAR PARKS DESIGN
Requirements for car parks built in the territory of Ukraine are provided for by the standard DBN V.2.3-15:2007 "Parking Lots and Garages for Cars". According to this regulation, the minimal dimensions for a car parked in storage shall be 5.0 m in length and 2.5 m in width.
It should be taken into account that DBN V.2.3-15:2007 applies only to a limited number of car models, mostly manufactured in the CIS countries. For other models, this standard recommends certain adjustments to be made for their specific fabrication dimensions. For this reason, the actual car dimensions have to be factored in when designing a car park.
As of July 1, 2014, harmonized European standards for building structures design (Eurocodes) came into legal force. These standards provide a more accurate description of stresses and loads on parking structures.
According to Eurocode 1 Part 1-1 (DSTU-N B EN1991-1-1), for parking zones where the total vehicle weight does not exceed 30 kN (≈ 3 tons) the specific value of evenly distributed weight load is 2,5 kPa, and the specific value for locally applied load used for a spot-on checkup is 7 kN
.jpg)
.jpg)
METHODS TO OPTIMIZE MULTILEVEL CAR PARK CONSTRUCTION
The use of standard design solutions for steel frames enables to efficiently address the issue of organizing engineering communications at the same level with flooring support structures, and reduce their structural depth, and, consequently, reduce the overall height of a building. This, in turn, reduces the height and cost of facades, or, alternatively, makes it possible to build more floors in a building of the same height. The most technically advanced solutions are multilevel car parks with intermediate storeys where two adjacent spans are shifted by half the height dimension measured between adjacent floors. This improves ventilation of a building structure, enhances structural rigidity, and increases the number of parking slots.
For parking structures, a reasonable option is to utilize a bracing scheme based on swing support of composite (reinforced concrete) flooring beams, with plates along with profiled flooring. Braced frames are mostly used when it is required to minimize the height of flooring beams or to minimize the deformability of the applied scheme. Other schemes are also applied — for instance, in which not only beams but also plates are made of composite materials, but they require the use of corrugated flooring (dimpled sheets). Swing support for beams is chosen because it is required to reduce the cross-section of columns and because it allows creating standard design solutions of floor framing and flooring with the same or lower the specific quantity of metal per structure.
The next method of improving design solutions is the optimal selection of types and crossing dimensions of beams. For a given column grid with main 18m spanned beams, the optimal beam crossing height is between 900 mm and 1100 мм (1 / 16-1 / 20 of span), but if we factor in the composite nature of materials, the same height does not normally exceed 800 mm (1/22 of span).
SPECIFICS OF RUST PROTECTION AND FIRE PREVENTION MEASURES
DBN V.2.3-15:2007 states that car park ventilation shall be organized in such a way that the concentration of pollutants does not exceed the maximum permissible levels as per GOST 12.1.005-88 "General Sanitary Requirements for the Air in Working Areas". The maximum permissible levels defined in the above document attribute the parking environment to Category "V" of aggressive gases as per DSTU B V.2.6-193 (valid until 2013) "Rust Protection of Metal Structures. Design Requirements". With due consideration for standard humid conditions, the degree of aggressive impact on the environment as per DSTU B V.2.6-193 (valid until 2013): • In closed car parks with heating — mildly aggressive. • In open car parks without heating — moderately aggressive.
Indirect requirements to steel structures fire protection in different-type car parks are stated in DBN V.2.3-15:2007, according to which the fire-resistance rating of above-ground closed car parks, as well as the permissible number of levels and square footage within the fire compartment, should be determined by the fire-resistance rating table, the number of levels, and the fire compartment size of above-ground car parks of the closed type. Irrespective of their fire-resistance rating, the stairway enclosure design in open car parks shall have a sufficient fire resistance class and fire spread limits that meet the requirements for stairway enclosures of buildings with fire-resistance rating II. Selection of this volumetric planning solution, which allows assigning a building with fire-resistance rating IIIa, helps to exclude the necessity of fire protection for the metal structures of a frame, except for the stairway enclosures. If composite flooring is used, it should be factored in as a corrugated board (with reefs) as the reinforcement of the plate. Considering profiled sheeting as reinforcement in assigning other fire resistance ratings is permissible only if sufficient fire protection is ensured. The required fire-resistance limits for structural items depending on the building's fire-resistance rating are determined in Table 4, DBN V.1.1-7-2002 "Fire Protection. Fire Safety of Buildings and Facilities".
The design of multilevel car parks with the application of Eurocodes helps to lower the cost of metal structures fire protection by 20%-30% as compared with the design under the domestic regulations. The effect is due to a differentiated approach to defining critical temperatures in steel structures.
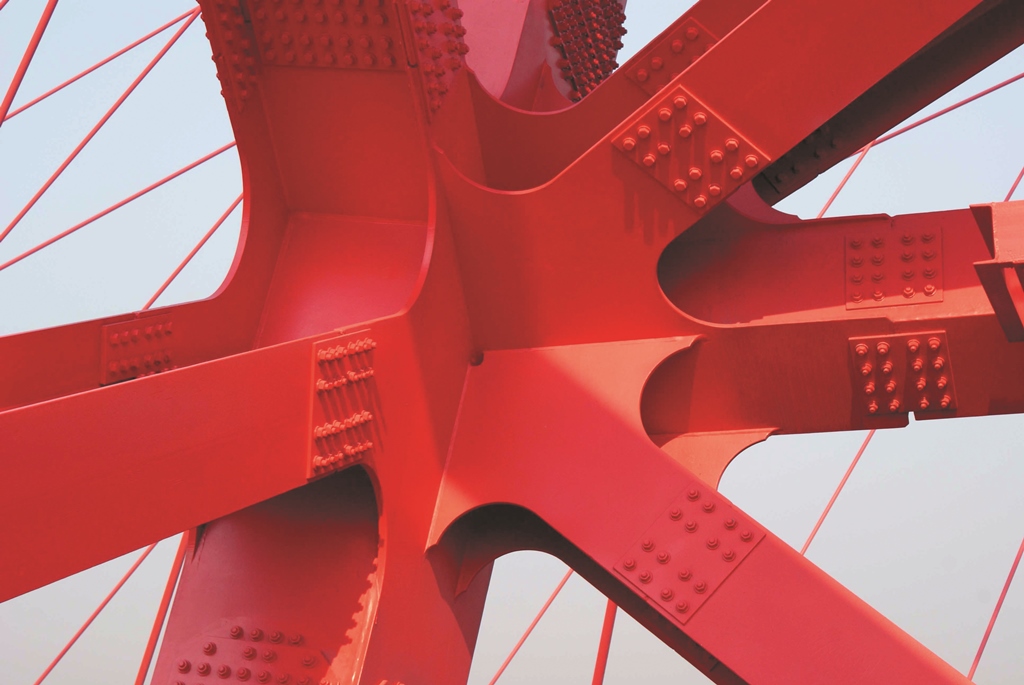